UNITED BLACK VULCANISING CEMENT/SOLUTION
Hall marks of the BVC manufactured by United Rubber are its excellent green [uncured] tack and it’s inseparable cured adhesion. The BVC could either be sprayed or brushed after adjusting the viscosity using suitable solvents.
STORAGE AND HANDLING PRECAUTIONS OF UNITED BLACK VULCANISING CEMENT/SOLUTION
Highly flammable, toxic, vapour harmful and fatal if consumed, contains petroleum spiritTo be kept away from heat, sparks and flameAvoid continued breathing of vapourAvoid direct and repeated contact with skinEnsure adequate ventilation when usedKeep container closed when not in useIn the event of fire, use water spray, foam, dry chemical or carbon dioxide.In case of leakage or spillage flush away area with water sprayTo be kept out of reach of children
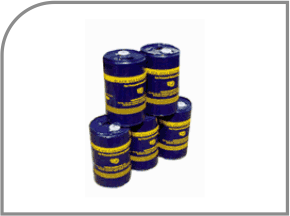
BLACK VULCANISING CEMENT – MODE OF PACKING
United BVC is available in 25 litres and 200 litres packing. Made out C.R.C.A sheets(cold rolled cold annealed), these drums are lacquered on the inside. It is provided with a 2″ diameter opening where threaded bung is provided for easy opening and closing. After filling BVC the bungs are capsuled and sealed for thorough protection of the contents. These drums are colourfully painted to provide the best aesthetic standards.
VULCANISING SOLUTION/CEMENT AND RETREADING PROCESS – HOW TO SECURE
BEST RESULTS.
In retreading, the buffed casing is brushed or sprayed with a Vulcanisable solution of Natural Rubber. This solution/Cement is made by dissolving the specially designed rubber compound in a suitable solvent.
The purpose of coating the buffed casing prior to capping of the Tread is to ensure that the uncured Tread Rubber is held in place before the built-up casing is placed in the mould. It has been established by research in the retreading field that cured adhesion of retreaded tyres where vulcanising solution is not used, is equal to those that have used the solution. Nevertheless, vulcanising solution has become part of the inputs for retreading, due to the fact that it provides the required building tack between the buffed casing and the Tread Rubber capped on to it.
VULCANISING CEMENT – WHAT IT IS?
Most of the ingredients used in the manufacture of Vulcanising cement compound are heavier than the solvent in which the compound is suspended. Therefore, at the time of storing the vulcanising solution, the constituent members of the solution which have higher specific gravity than the solvent used will have a tendency to settle down at the bottom of the container. Thus the top portion of the vulcanising solution kept in a container will miss some of the ingredients required to bring about vulcanisation.
Likewise, the bottom layer of the solution will be lacking in rubber content since, specific gravity of rubber is less than that of most of the chemicals used and also due to the fact that rubber and the solvent used have more or less matching specific gravity. Hence it is very essential that the vulcanising solution is thoroughly agitated or stirred before application on the buffed casing so as to make the solution homogeneous and to ensure balanced distribution of all the ingredients used in making the solution.
MODE OF APPLICATION
Prior to application, vulcanising solution supplied by various manufacturers may be diluted using rubber solvent. Use of Vulcanising solution without proper dilution can create retreading failures. A thick coating of vulcanising solution applied on the buffed portion with a stiff brush will take more time for drying. This is because rate of evaporation of solvent from the thick coat of solution will be very slow. Here also, the evaporation may be confined to the surface, leaving wet solution inside. In such a case, at the time of curing, the solvent in the solution will form big blow-holes and blisters at the base of the tread, giving chances for tread separation. Sponginess and porosity at the base portion of the tread are the other defects resulting from incomplete drying of solution which was applied too thick.
If solution is applied with a spray, it is essential that the same is suitably diluted to the required consistency, using a rubber solvent. While spraying the solution, care should be taken to see that :-
1] Moisture should not get mixed up with the solution to be sprayed
2] Air used must be dry and free of oil and similar contaminates as these foreign materials will lead to retreading failures resulting from poor adhesion.
Usually, Vulcanising solution supplied by the manufacturers is to be diluted by adding an equal quantity of solvent.
The solvents commonly used for diluting the vulcanising solution are either HP Solvent 1425 and SBP 55/115 [BPCL] or their equivalent.
Care should also be taken to see that the solvent used for diluting the Vulcanising solution is free of contamination from oil or any other adulterant.
The most simple way to test the purity of the solvent is to dip half portion of a clean strip of white paper [about one inch wide] into the solvent. The strip of paper after it is withdrawn from the solvent, may be allowed to dry. If the area dipped in the solvent shows a dark colour or any residue or discoloration after drying, the solvent should not be used. Similarly, two strips of paper can be dipped in two different types of solvent to find out which dries fast. Solvent contaminated with oil or other adulterants will take more time for drying.
Application of Vulcanising solution to the buffed tyre should be done taking maximum care and caution. The buffed surface should be clean and completely free from buffed dust. In order to prevent contamination with dust and other foreign matters on the solutioned surface, solutioned tyres may be kept in separate dust proof rooms.
In order to ensure proper building tack, it is essential that adequate drying time is given to the solutioned tyre. The drying time of the solutioned tyre is dependant on factors like climatic conditions, humidity, room temperature etc. Although high humidity will slow down the drying time, it will not have any impact on the cured adhesion.
HOW TO TEST THE QUALITY
A fast and simple method, suggested by ‘Retread Research Centre, U.S.A.’ can be tried out for assessing the quality of the vulcanising solution. This is done by brushing several coatings of solution onto an aluminium foil approximately 6 inches x 8 inches in size. After allowing the solvent to evaporate, fold the aluminium foil with the dried solution on the inside. Thereafter place the aluminium foil inside a tyre next to the crown area and between the tyre and the curing tube. When the cure cycle is completed, remove the aluminium foil and unfold it. The solution can be judged O.K. if it is cured properly.
The degree of viscosity or thickness of vulcanising solution may vary from supplier to supplier. Hence it will be a good practice to assess the difference in consistencies of various brands of vulcanising solution. Such a comparative study will help to determine the extent of dilution required for each brand of solution. The equipments needed for conducting this simple test are:
1] A 100 CC Glass Beaker the bottom side of which is tapered and provided with a hole 1/16″ diameter.
2] One stand and clamping device to hold the Beaker firmly.
After fixing the Beaker between the clamps of the stand, fill the same with the solution up to a particular level, keeping the bottom hole closed. Then allow the solution to drain out into another beaker which is kept below.Note the time taken for complete transfer of solution from the tapered beaker to the one under it. Repeat this test for various brands and find out the time taken in each case. Solution or Solutions which take more time for draining out will be thicker than the ones which take lesser time. Hence it follows that the former ones need more dilution than the latter.
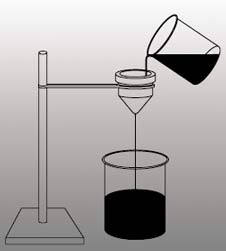
SUMMARY
Utmost care need be taken in the selection and application of vulcanising cement to obtain optimum bonding of the retread. Always use consistent viscosity solution with the same rate of drying. Quality of the cement may be checked occasionally with the methods given above.